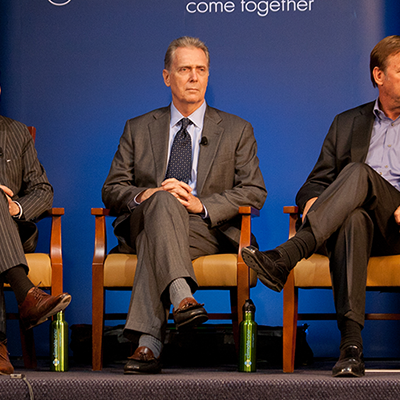
Building Green Cities
Guests
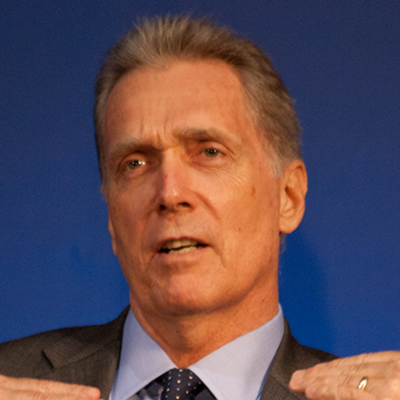
Michael Deane
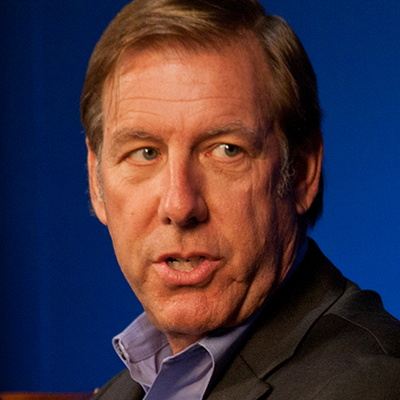
David Gensler
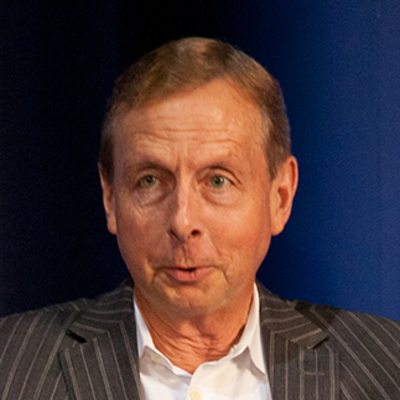
Craig Hartman
Summary
How are some of the largest building design and construction firms meeting client goals for more efficient resource utilization and cleaner built environments?
Full Transcript
Greg Dalton: Welcome to Climate One at the Commonwealth Club, I’m Greg Dalton. Many companies these days promise their customers and employees they’re doing something to go green. In addition to product labeling and advertising, corporations are increasingly doing business in buildings that more efficiently use energy, water, and other resources.
In the next hour, we’ll explore how some of the biggest architecture and construction firms in the country are helping American businesses reduce their carbon footprint. Buildings account for about a third off all energy consumed in the United States and about a third of America’s carbon pollution. In China and other developing countries, mind-boggling numbers of new buildings are being constructed that will have even bigger disruptive impact on our shared global climate.
Here, with our live audience in San Francisco, we have four executives who design and construct skyscrapers with their own bare hands and design -- other buildings around the world. Michael Deane is chief sustainability officer at Turner Construction based in New York. David Gensler is executive director of Gensler, the country’s largest design firm, which is headquartered here in San Francisco. Craig Hartman is a design partner with Skidmore, Owings, & Merrill or SOM, a venerable architecture firm. And Phil Williams is vice president of Webcor Builders, which is building the Transbay Terminal nearby and many other buildings.
Please welcome them to Climate One.
[Applause]
Let’s go alphabetically. I want to get you to introduce yourselves -- where you’re from.
Craig, let’s begin with you. You’re here from San Francisco. Tell us about your home and what kind of energy footprint your own home has.
Craig Hartman: Well, that’s -- that is a very private question. (Laughter) But, I think our footprint, happily, is fairly small, I think. We actually -- we live in Marin, so that’s maybe a slight embarrassment. We don’t -- I can’t walk to work. I work near here in the city. However, I drive an electrical car, a Leaf, back and forth.
[Applause]
Greg Dalton: Yeah.
Craig Hartman: Thank you very much. And we power our entire house with photovoltaics on the roof. So we are hooked up to PG&E, so our only evidence of this power is the reverse turning of the meter, but nevertheless, that’s our kind of lifestyle. And my daughter is here, and my wife are extremely concerned about my water use, so brushing your teeth and turning the water off very quickly and those kinds of things -- but so, yes, that’s a kind of a quick synopsis of my personal lifestyle.
Greg Dalton: Great. And David Gensler, you’re from Los Angeles. Do people conserve energy in LA?
David Gensler: Oh, yeah.
Greg Dalton: Okay. [Laughter]
David Gensler: No, I’m from Los Angeles, but I actually probably have a fairly large carbon footprint, because I fly most of the time. I’m on the road 150 days a year. We have 43 offices around the world. And so this afternoon, I leave for Doha and come back, and then I go to Dallas, and -- I’m all over the place. So, my carbon footprint is not quite as low as yours; I apologize.
Greg Dalton: And airplanes are big --
David Gensler: But it’s public transportation.
[Laughter]
Greg Dalton: That’s an interesting…
Michael Deane: And there are interesting facts about how little apparently per passenger these things…
Greg Dalton: The plane will fly anyways even if you’re not [crosstalk]
Michael Deane: That’s what I said. I’ve never been in an airplane that wasn’t going anyway.
Greg Dalton: Yeah. And, Michael Deane, you’re from New York. Tell us about your energy footprint.
Michael Deane: Wow. I live in a colonial house that was built in 1930.
And it’s got a great roof that faces dead south, and I’ve always wanted to put solar panels on it. But instead of going for the green bling last year, I had insulation bling, because it had no any insulation in any of its exterior, so -- around the walls and in the attic, and my heating bill went down by 50% instantly. So, that’s it -- that was a good investment. The other thing that I do is I yell at my children to turn off the lights. It was a trick I learned from my father. [Laughter] And other than that, if you take a minute, when -- my kids are teenagers now. And when they were little and they found out about my job, and they said, “Daddy, your job is to save the earth, right?” And I said, “Yes, girls, it is.” [Laughter] And so then my oldest said, “So, that makes you a hypocrite, right, Daddy?” [Laughter] Because of the discrepancy between what I say and what I do. So none of us are perfect, but we try and recycle and all that stuff.
Greg Dalton: Yeah. Me either. Phil Hartman, you’re here in the Bay Area.
Phil Williams: Yeah. Phil Williams, I live in Walnut Creek [crosstalk]
Greg Dalton: Phil Williams, sorry.
Phil Williams: That’s fine. I’ve got one of those pick your climate, you know, in terms of the Bay Area. We’re a little bit like a mixture up here. We’ve got a nice, you know, late ‘60s rancher that holds of a different era. I actually have a bomb shelter in my backyard, because it was built in 1963. So, depending upon which era you are in, there were various, you know, issues, but they’re all important ones. We’ve done more like a combination -- a little hybrid on the car, re-insulation, re-windows, turned off the heating on the swimming pool, you know, figure a good brisk component works, and so a little combination of everything.
Greg Dalton: All right. So, there’s where you got your green cred here as established. Let’s talk about LEED that’s a term that a lot of people hear. Many people may not typically understand what it is. And then we’ll talk a little bit about sort of the pros and cons around the -- so, Craig Hartman, briefly describe what is LEED -- the Leadership in Excellence and Energy and Environment Design, yeah.
Craig Hartman: You’re asking me to describe this?
Greg Dalton: Yeah.
Craig Hartman: All right. Well, I’m sure 99% of the people in the audience can describe this better than I.
But nevertheless -- so, you and the audience know that LEED, Leadership in Energy and Environmental Design, [crosstalk]…
Greg Dalton: Environmental Design -- yes, see, we talked about it.
Craig Hartman: -- is a kind of a prescribed list of things that one can do to design buildings intelligently, in a very holistic way, to look at energy consumption, water consumption, where the building is placed, how is it oriented, what kind of innovation you can bring to a building in order to make it perform better from the point of view of energy and water consumption.
And then out of that process comes a ranking just like the Olympics, almost, where you’re a LEED-Certified or a LEED Silver or a LEED Gold or a LEED Platinum. So it’s a very easily, perhaps understood -- maybe the mechanics aren’t so understood, but certainly these branded steps of Certified through Platinum is something that’s very easily, I think, understood by many people. And so, it’s become a very common kind of a metric or yardstick for the performance of buildings specifically. But now, happily, also has gone much broader than this to large-scale neighborhood developments, which is where the real positive -- the major impact we had is where you think not just about the building itself, but where it’s placed, is it -- can you walk from your office to your -- like me to office from the house and so forth. So, as you know, it is a measuring -- metric system that can be used to quantify or to begin to suggest how well buildings perform environmentally.
Greg Dalton: Phil Williams, does it cost more to get LEED Certification than regular --
Phil Williams: You know there’s a nominal fee that you have to pay to be able to do that. But for instance, in San Francisco and in California, it’s virtually the law, if not the marketing component for it. The design doesn’t necessarily have to cost any more. We’re able to deliver LEED Silver projects here in San Francisco at virtually no additional cost on the construction site.
And many times, Gold is well within reach as well. And in fact, it can’t cost more to deliver Gold office building in San Francisco because that’s the building code that was established in January that many people here, including myself, helped write. It’s not an arbitrary thing that comes from the outside. It’s really an industry from the design, engineering, and construction, now, I hate to use the word ‘policing;’ it’s really being responsible for the products that we build. So, I tell people it’s not bolted on; it’s built in. It doesn’t have to cost more. Intelligently use your resources, and it works very well.
And one of the things that’s interesting about it is that we’re fortunate here in California. But because we can offer leadership position, it’s really become the standard for commercial real estate. It’s not about energy, and it’s not about does it cost more, it’s how was it -- can I be competitive in the marketplace? And it’s been extremely valuable because new buildings drive existing building portfolios, which is extremely powerful. In the last three years, how many new buildings did we build here in California, let alone anywhere. But it -- all it takes is one new building driving the existing building portfolio to also gain LEED, because there’s no one more competitive than real estate. And that’s what I like about this business.
Greg Dalton: David Gensler, what percentage of buildings that Gensler designs are LEED. Give us a sense of the market percentage. I read recently there’s 2 billion square footing of LEED-Certified buildings in the United States. It sounds like a lot, I don’t know proportionately what that means. Give us [crosstalk] --
David Gensler: I don’t know the percentage off the top my head, but I know we have about 186 million square feet of LEED-Certified buildings. We’ve got $38 billion in construction that we’ve done. So, we have a tremendous portfolio. We do 5,000 projects every year for over 2,000 clients. So our footprint in terms of the building -- built environment that we touch is extraordinary, and we have a tremendous commitment to LEED.
We have more LEED-accredited professionals than anybody in the world.
Greg Dalton: Michael Deane, let’s get you on this, too. The market drivers, you know, is this something that’s happening? Tell us -- talk about the market drivers. Is it because tenants come around and say, “Hey, where’s the LEED certification? This building recently got LEED slapped on it.” So, is that something that’s become de facto in the market?
Michael Deane: Well, it really has, and as Phil was mentioning before, it’s virtually synonymous with Class A commercial office. And people -- USGBC did a wonderful job of --
Greg Dalton: The United States Green Building Council, which --
Michael Deane: The U.S Green Building Council, which is the creator of LEED -- did a wonderful job of marketing it so that it became synonymous with environmental performance and energy efficiency and water efficiency and healthy indoor environment. Those are all the things that people want. So when they’re told they can have that, and that a LEED building is a third-party certification of the fact, not just me saying my building is green but some independent entity saying my building meets certain standards, then people want that. For the last four years now, over 50% of our work total across every market sector has been LEED, and last year was 58%, and we do about $8 billion work a year.
Greg Dalton: So, is LEED -- it sounds like is an industry standard. But is it really the best standard or is just the best known? David?
David Gensler: I don’t think it is a panacea for defining what is a good building at all. I think it is an accepted standard that we can all use to measure the performance of buildings to strive to improve the performance of buildings. But it isn’t, by any means, perfect. It’s got -- it’s, in effect, a proxy for performance. Many of the -- it has a point system, so you earn points for every aspect of your design.
Some points are probably easier to get than others in terms of the economics, and so people tend to go for those kinds of points. Other points have much greater impact on the actual performance in terms of resource utilization and carbon footprint and energy and water than others. So it’s not, actually, I think, an ideal solution, but it is the one that we’ve all kind of standardized on, so it’s better than nothing.
Greg Dalton: So, it’s possible to have a LEED building but it really isn’t that efficient.
David Gensler: I think, unfortunately, what we’re finding is that many LEED buildings that are modeled to a level of performance that we expect don’t turn out to deliver that level of performance, because when they’re operated, they don’t have the outcomes that we anticipate.
And one of the things that USGBC is doing now is starting to develop methodologies that will require reporting, that will require ongoing monitoring of building performance, and allow us to continue to enhance the performance and operation of the building.
Greg Dalton: Michael, do [crosstalk] --
Michael Deane: I think it’s important to understand as has been said that LEED -- the LEED rating system is a checklist. It’s the proverbial Chinese menu. And to say that a building is or is not efficient because it’s a LEED building misses the point. LEED awards its certifications based on accumulating points and you can do that in many different ways. And some owners will emphasize energy efficiency or water efficiency. Other owners will emphasize indoor environmental quality. So it depends on what’s important to the client, and then it’s also important what the budget is, and sometimes, there are points that are achievable at a lower price point than others. So, there’s different ways of talking about how a building is efficient.
Greg Dalton: So, Phil Williams, can LEED be used to green wash?
Phil Williams: You know you can get, I guess, the lowest level of certification that you -- if you needed to. And it’s a pretty big mature market these days. And I think, since it’s simple in its context, which is part of the reason that it works very well.
One of the things that we’re seeing though is that even though it might be the U.S. Green Building Council, it is the de facto global standard. I think it really speaks to the value of U.S. engineering, design, and construction and architecture that we may not have been the first standard, whether it’s BREEAM or Green Globe’s, but the fact is is that it creates a universal standard for property, which is important.
I also think it’s -- LEED recognizes that it is an evolving standard and is a consensus standard. It’s not the most aggressive standard. I mean you could have a net-zero energy building; you could have a living building challenge building out of a Cascadia in the Northwest. And the good part is these standards try not to compete with each other; they recognize that each have a place in the marketplace.
One of the things that I also like is that LEED didn’t try to create new rules; they accepted the ASHRAE, American Society of Heating, Refrigeration, and -- Engineers standards. And as new standards are developed for interior building healthiness and wellness or environmental product disclosures that really provide transparency for building products, it’s maturing. And like anything, we’ve all got kids or we wish we were kids, but the fact is you get better, right? And maybe you don’t get faster, but you get better, you get wiser, and you get more mature. And I’m extremely confident that LEED is still going to continue on its good trajectory, and that it isn’t going to get bogged down with some of the other kind of politics. Because it is an NGO, and I think that’s important.
Greg Dalton: But the LEED’s -- we’re supposed to come up with a new version. It was postponed from this year to next year. And they’re having some challenges --
David Gensler: Yes.
Greg Dalton: -- about how far -- how much the industry can adapt at a certain phase. David Gensler?
David Gensler: Well, look, I think they have a long-term aspiration to encourage and incent the marketplace to get better and better.
And that’s the right objective. How quickly they can go is a challenge, because if they get too far ahead of the marketplace, then the market won’t pursue LEED certification. They won’t pursue LEED Gold or Platinum.
Everybody has a place in the marketplace. Some buildings are going to focus on getting the highest standard possible, you know. They’re trying to do the right thing, and I think as Phil said, you know, the long-term, they will encourage and provide a vehicle for the marketplace to improve itself. Long term, they want to be net positive, they want to be net zero. Right now, we’re not there yet. As a marketplace, they’re just far enough ahead that they force the industry to stretch to perform at a higher level than they would without them.
Greg Dalton: And one of the weak points or critiques of LEED is that it’s -- it’s sort of -- as a building is designed and built, not as it’s operated. So let’s talk about the operating results can be different than -- who would like to take that on? Michael Deane?
Michael Deane: Well, it’s huge. I always make the analogy to an automobile. You can build a high-performance automobile, and if I don’t know how to drive and I run it onto a tree a tree, I can’t blame the car. It’s me; I’m the driver. So, what USGBC and LEED are recognizing is that it’s not just the bricks and mortar and the mechanical systems, it’s how the building is operated over its life in service. And so, we’re spending much more time thinking about that. We’re thinking about costs and benefits in terms of total cost of ownership, not just how much it costs to build it at first, and in terms of operation, the energy efficiency, the indoor environmental quality, and water efficiency are going to be a function of how the building is operated over time. So, there’s more emphasis on measurement and verification and real-time interaction with the building to make sure that it is performing up to the standards that it was designed and built to.
Greg Dalton: And that’s a big deal to start and operate -- you know, it’s easier to sort of, “Okay. Buildings design, done, coded, got your stamp,” but this is going to be more of an ongoing monitoring auditing process -- sounds more complicated?
David Gensler: Commissioning and operating a building is a complex system, and the -- you know, the in-place community that has been used to operating buildings for the last hundred years is probably not -- got the skillset required to operate the buildings of the future. They’re much more technologically-oriented. Their requirements for building engineer, you know, 10 years ago or 20 years ago are different from what they are today. And to be honest, I don’t think it’s the sexiest career path, so you’re not attracting, you know, the top technological talent to be a building operator, a building engineer.
Greg Dalton: Craig Hartman?
Craig Harman: I think that however the culture is moving ahead in this direction. And, for example, policy does often drive these kinds of innovations, and certainly, I guess, true here in San Francisco, where we have -- we’re probably are used to kind of living in a place that is pretty unusual than the rest of the world in terms of the grassroots as well as the political embrace of environmentalism. And so, one of the policies that the San Franciscans, what we had with is reporting of energy consumption, water consumption of buildings here in the city. So, it’s going to become actually part of the process of owning and operating a building that you have to report these. And when these things are reported, when they’re made visible, of course, then the competition, you know, as described, you know, really begins to kick in. You know, my building is a Hummer and my -- the other building is a Leaf or a Prius or something. So, this does have a major, major impact, and I think ultimately in the sort of an acceptance and then ultimately, the codification of these kinds of systems.
Phil Williams: I’m just going to mention that a little bit, and the fact is is that I think we’re at the stage when we’ve added a lot of technology but they’re independent systems in building.
And I think we’re about -- going on your analogy of a car -- we’re about to have a car that’s really integrated, that’s more efficient than it used to be, runs quieter, more efficient, less tune-ups, and I think so as technology -- and where part of that here in Silicon Valley starts to merge these items. The buildings are going to rely less on Bob, the ex-Navy guy who ran the destroyer to make this thing work. Because that’s how a lot of buildings are run today. It’s personal experience. The building manager may come and go, but the chief engineer is the lifeblood of the building. I think that’s some of the interesting part of it.
What’s even more exciting is that some of this monitoring and some of the LEED work means that new technology migrates from new buildings to existing buildings, not the other way around. And to me, that’s the exciting component, because that’s the 98% of the buildings. We’re just making the best buildings better when we go from Gold to Platinum, but the ability to take some of that wireless technology and add direct digital controls to a project that was built in the ‘60s, ‘70s, and ‘80s that had pneumatic controls without disturbing the tenants or walking on their desk or pulling ceiling tiles. I mean, no one can tell me that wireless is a problem. Every one of us has a wireless device -- whether it’s a wireless micro or a wireless telephone that we rely on forms our lifeblood of business. That’s where this building market is going, and that’s where the technology-driven world, the LEED world, the energy world is really going to provide some platforms for stuff that we now consider, you know, our cell phones now are going to be a digital wallet fairly soon. That’s what our buildings are going to turn out to be as we transform them -- existing and new.
Greg Dalton: And technology can do amazing things, but listening to this, I’m thinking about home entertainment centers, which we probably all have and we probably -- maybe we know how to operate, but they have features and functions in complexity way beyond what the average person can use.
And thinking about buildings that have all sorts of cool stuff, but people don’t know how to use them. So how do you -- you’re getting -- can you get ahead of the culture of (crosstalk) --
Craig Hartman: Maybe just to step back for a moment -- beyond -- pre-technology is a -- there’s some very, very basic things about the way that we can design -- we should design buildings that respond first of all, to the way that relate to the sun, the way that we harvest the sun’s energy, or simply provide the best aspects of sun heating in the winter, shaded, you know, areas in the summer time. The first thing is to design buildings intelligently so that they’re passively designed to adapt to their environment. And then the bells and whistles come later, but I think we get wrapped up in this sort of extraordinarily high-tech, you know, ideas about the way to make buildings perform, when in fact the structure of -- they are very basic simple things. Starting with, by the way, living, unlike me, in the city, walking to work, you know, having a dense, compact walkable places, having buildings that are oriented the right way to the sun and the wind -- those are the basic things we should doing.
Greg Dalton: But why aren’t they happening? If they’re so basic, why aren’t developers and city planners already doing this? Because they don’t think about energy and passive -- is it --
David Gensler: Well, if you look around the world, there are some countries where they’ve always practiced passive sustainable strategies in their designs. The materials they use, the orientation of the sun, the use of air flow and, you know, trade winds have all been really important to many cultures. We, I think, in the West, probably kind of dominated the environment and didn’t have to consider that in a lot of what we -- our existing city plans. But if you look at urban planners today, they’re taking that into consideration much more heavily than they did 50 or hundred years ago.
Michael Deane: Yeah.
Greg Dalton: Michael Deane?
Michael Deane: I think -- if you think about one way of looking at it is before the advent of mechanical systems, all buildings were essentially net-zero buildings. And it’s the classical study of architecture. If you remember when architecture was one of the fine arts, I think what happened was we got enamored of technology. And we realized that you could build a glass box unconditioned to space with machinery at a time when we weren’t so aware of and concerned with resource consumption and the effects of that. And that now, I remember, a year or two ago at Green Build, which is the annual meeting of the USGBC, all of the education sessions were about how complex and technically advanced buildings were getting. And I got to the point where I was thinking, “don’t show me that you can make it more complicated, show me that you can make it simpler,” right? So I think if we can go back to a time when you care about sighting and thermal mass and orientation and natural ventilation and natural light, then you’re going to get a better building.
A colleague of mine who’s building a net-zero building up in Sacramento said you can make any building net-zero if you’d slap a lot of PVs on it, but it’s not a very efficient way to go about it. So the first thing you do is you work as hard as you can to reduce the demand of the building, and then -- in this project that I’m referring to, it’s for the Sacramento Municipal Utilities District. It’s a 200,000-square foot building, so it’s a real building. They’re getting net-zero for an 8% cost premium with a 12-year simple payback, and for an institutional owner, that’s great. And what they did was they maximized the efficiency so that the building starts out needing 50% less energy than a standard building. And then they cut their PV bill by a million and a half dollars, because they made the building efficient to begin with. So, that’s I think, where we need to start to head.
Greg Dalton: Is it ugly? I mean --
[Laughter]
Michael Deane: You know, it’s a very handsome office building. [crosstalk] It is an office building and a facilities maintenance yard, so it is as good as you can get with it.
Craig Hartman: Okay. But it’s a very important point, because one of the first Platinum buildings in California is also one of the most ugly.
And I have to say that long-term, I think that sustainability starts with making buildings that are beloved by the community and making buildings that 50, 60 years from now that those of us here will want to renew them, want to remodel and restore them somehow, as opposed to tearing them down and starting all over again. So, that’s a very, very important point.
The other thing is just -- to be getting back to this question about technology versus simple passive thinking, is that a room like the one we’re in, this is like probably a 20-foot high ceiling, and you’ll notice those squares at the top are where the air-conditioning comes in. So the air drops down and is exhausted back to the same ceiling. So we have to air condition this entire 20-foot high space to make those of us who are sitting down here at the lower six or seven feet comfortable. Now, that’s kind of a backward way of thinking. So, very simple devices are what we call displacement cooling where you actually introduce the cool air from the floor. We air-condition where we cool only the lower 8, 10, 15 feet that we’re occupying -- who cares what the upper, you know, 15, 20 feet -- 15 feet above. And so, we’re doing this more and more with buildings and in large public spaces like at the San Francisco International Airport Terminal.
We did this many years ago, and it consumes about 30% less energy than the other terminals -- I’m sure not the more recent ones of course, they’re doing much better than that David’s involved here with, but the…
David Gensler: Absolutely.
Craig Hartman: But the -- and the Cathedral in Oakland are the same thing. We’re now doing these in office buildings, and one that Phil’s probably been building are shortly across the street -- a simple 20-story building which we are using displacement cooling in every floor. The ceilings are 10 feet high. We are conditioning really the only lower seven or eight feet of that. So we have 10%, 15%, maybe 20% of the volume of the space doesn’t rise the same level of conditioning or drop, in this case, to 70 degrees. So therefore, we’re really only conditioning about 80% of the building. While you’re getting the value though of the light to the tall windows, so it’s -- these kinds of just very simple thinking about the way you introduce air and light in the buildings is where we need to start with these things.
Greg Dalton: And are developers seeing this? The people who build large amounts of office space in the United States and elsewhere, do they see the economics in this? Is this the developer’s building?
Phil Williams: I mean, yeah. The -- whether it’s raised access or displacement, it’s really just like a car. A building is designed to have people in it and to do their work effectively. And now, we just have more tools at our disposal -- whether it’s displacement ventilation, whether it’s variable refrigerant, whether it’s natural ventilation and day lighting, the fact is that we can reinvent old things and still keep the ones we’ve got. So now, we’ve got the right tool for the right purpose, and we’re not afraid to use it.
David Gensler: I think the raw economics of energy right now are driving a lot of innovation. When you have a $10-a-barrel energy, it’s a very different incentive to use energy efficiently than when you have $100 a barrel energy. And right now, we, all I think and feel a sense of concern that it’s not just going to be a hundred; it’s going to be $200 or $250 a barrel.
Greg Dalton: But petroleum doesn’t really power electricity that goes in the buildings, right?
David Gensler: But all -- the entire cost of energy is a fungible market. You know, there is geothermal energy, there is -- but you know, coal and carbon…
Greg Dalton: Now a ton of natural gas.
David Gensler: -- natural gas. There’s all kinds of energy sources, but at the end of the day, the price of energy is a market that moves and ebbs to where the, you know, the most efficient use of the energy that we have at our disposal at a price that you can get. So you see, you know, a lot of people are converting to natural gas now because it’s much more cost-effective. But there’s still a tremendous amount of, you know, fossil fuels that are being pumped out of the ground and sent across the world to power cars and other things. When you have $4 a gallon for gas, people get more sensitive to the, you know, the mileage that they’re going to get out of the car. They’re not going to buy, maybe a 12-mile a gallon vehicle; they’re going to buy a Leaf or a Prius.
I mean, you saw that happen. So, the market does play a role. The other thing that’s happening is regulatory-driven incentives and penalties that are driving us. So, between the market and the regulatory incentives and penalties, you know, we’re seeing tremendous amounts of innovation that you wouldn’t have seen, you know, 20 years ago because there weren’t those things in place. The economics didn’t drive us there and the regulatory environment didn’t drive us there.
Greg Dalton: Phil Williams?
Phil Williams: One of the things that -- and I don’t mean to change the subject, but I need to hear a little bit I think, only because we’ve got a little energy-centric. And energy is a big part of where we see this process going. But one of the things that you’ve talked about market drivers in energy and development, I think there’s a big push in the consumer side. In the consumer, I mean the people in the buildings, about improving the quality of the environment, not at the sacrifice of comfort.
I think, you know, part of this innovation and research is going to be the materials that you put in our buildings, the longevity of the materials, what’s the sourcing of those materials, what happens when those materials get done. It goes back to, you know, a little bit for design, a little bit more for construction, a little bit more for operation, and then a concentric wheel of what’s the value that the product was put there to deliver in the first place -- the productivity of the people. And that’s where I see a huge push that is part of the sustainability component. That yes, it’s water, and yes it’s energy, and yes it’s gas and transportation. But we’re putting people in buildings where they’re living a considerable amount of their time. And what I like about it is that it may be driven by the commercial world, it may be driven by LEED or Living Building Challenge or Red Lists or whatever those components are, but whatever starts in the commercial world migrates to the personal world, right? Computers were in your office before they were in your home. Telephones were in the office before they were in your home. And the better building materials are going to be in your office before they’re in your home.
And so the ability to all of us as professionals recognize that we have an obligation -- now we actually have more work to do that we did before. And I think there are some standards out there that are going to be developing. They’re going to be supplemental to LEED -- go back to LEED side that are now going to give us visibility and transparency in building materials. And whether it’s part of this concept of life cycle analysis that’s yes, it’s about the energy; yes, it’s about the water; yes, it’s about how long it’s going to last. Is it a disposable commodity, you know? What’s in it? And when we’re done with it, what happens to it?
Those are the kind of things that probably actually get me more excited, because we got the current standard which are all in favor of, but we’re rapidly moving to a much more comprehensive, much more transparent, much more decision-made data-driven process. And it’s not judgmental. I don’t think anybody should say this is good and that’s bad. It’s like cereal. I can eat the organic granola, or I can have Super Choco…
Greg Dalton: Coco Puffs?
Phil Williams: … yeah, Coco Puffs. I can tell what I’m eating. I’m not saying which one is good or which one is bad, but now I know, and I can make my own value decisions. And that’s what we want to give to architects and clients.
Craig Hartman: That’s right. It is definitely -- energy always -- we focus this question because energy is the source -- primarily in our consumption, energy is the source of carbon in the air, and therefore greenhouse -- you know, gases and climate change. And so, this is a huge, huge issue for us as a human species, obviously.
But water is equally an issue, and the work that I think we’re all collectively doing right now is focused on ways of intelligently using water to minimize the unnecessary consumption of potable water, to reuse it as much as we possibly can. The city of San Francisco is very much a part of this as well.
And to also pick up one of Phil’s point about the other big step to getting towards what we call a net-zero impact, which of course is an aspirational idea and new generations are very aspirational, but a long way to get there.
But the idea that with our -- or the things that we make, first of all, can or value for long term for communities. And secondly, that they’re adaptable to change and that we can make places that are flexible for all kinds of uses. And we are now writing manuals not just for the way you operate your buildings from a mechanical point of view but also, for example, in laboratories that are in universities, writing manuals on a system of flexible arrangements for the labs that could be easily changed without throwing things away, and these pieces can be recycled. So, the idea that we can recycle components for our buildings without even necessarily taking them off site is, I think, those are the kind of things we need to be focusing on.
Greg Dalton: Let’s pick up on the resilient and flexible aspect of that. We’re in an era where the weather’s changing, the climate is changing. We’ve seen some amazing droughts and storms around the world recently. So, you’re designing buildings that need to be around for 30, 40 years, and your assumptions about the weather in any particular place are going to change dramatically. How do you build and operate a building in the era for the era of climate disruption where things are going to get kind of screwey?
Craig Hartman: You can’t know the unknowable, of course. And what we’ve seen in the last few years, of course, is that what we thought about weather patterns is quite surprising. We’re surprised in what we don’t know. And things about like the fact that we’re now having more of a snow pack in Siberia and that’s causing all kinds of disruptions. So, I don’t think we can say for sure in the next 60 or 80 years what the weather will be like in San Francisco, for example. We have a great thing here. We have the ocean as our air conditioner, but nevertheless, we can’t say for sure. But what we can do is respond to what we know and to make buildings that can function in multiple ways.
And so, we’re designing our buildings now so that they are -- they can breathe but they also can work with these systems we’ve been talking about. And certainly, we’re even look here in San Francisco, of course, in California at the fact that our earth isn’t -- doesn’t just sit still either. And so, we have earthquakes and -- so, the work that’s going into design of buildings now that can not only withstand, but remain operational after a major earthquake is also a big part of what we’re now doing both here and in other places -- China and so forth where everywhere there are deflections of tectonic plates.
Greg Dalton: You mentioned China. Where -- you work around the world. You all operate somewhat internationally. Where’s the greatest innovation happening in building and ideas? Is it in Europe? Isn’t it China’s doing things at scale and pace that no one else is? Where are the things that are happening that are really exciting? David Gensler?
David Gensler: Well, I think more is getting built in China than anywhere in the world.
Greg Dalton: Mind-boggling.
David Gensler: Some -- I mean the statistics there are they are building a city the size of a million and a half people a month, you know. So there’s tremendous innovation. The quality of the construction is improving. The systems are improving. The buildings that you see that are being put up today are world-class buildings.
Greg Dalton: A lot of the roads in China are better than the roads in the United States.
David Gensler: Ten or 20 years ago, even though there was still a tremendous amount of activity, it was much more rudimentary. So I think that’s a marketplace that we’re seeing tremendous innovation. And for a designer, I don’t think that there’s a better environment than where the world is getting built in the developing world, Asia in particular. Also, South Korea seems to be, from my experience, a tremendous hotbed for innovation, particularly in terms of technology systems and buildings.
Greg Dalton: Are you doing the big airport there?
David Gensler: In China, airport, yeah.
Michael Deane: Others -- well, I would say that Europe has been way ahead of the world for the last, you know, two or three decades in terms of policy on these matters.
And for example, even as of like 25 years ago, Germany had policy laws in which you could design an office building that would have no more than – I think it was 25 feet from an occupied building to glass for daylight. And so I think -- so this hasn’t really been about policy, but in terms of actual implementation and making driving innovation, no question. It’s where things are built -- that’s right, now in China, for sure.
And so the first building that I did in China was in 1993 in Beijing, and it was the Industrial and Commercial Bank of China’s headquarters. At that time, after winning the competition to design it, we started touring the facilities and looking at what resource were available. So we went to the steel plants. The chairwoman of the bank wanted steel as opposed to concrete. She saw this as being a very modern idea. All buildings in China are made of concrete, basically. So, we started touring these plants. We found that all the steel was being used for tanks and for trains and so forth, but not for buildings. Likewise, there was no glass being produced.
And today of course, now it’s absolutely the opposite. Now, China is at the front for not only adaptation but it’s even production of these major systems we talked about in the previous panel about photovoltaics being produced there. So, it’s definitely without question, because of the economic activity there, it is really a huge source of the ability to apply innovation and all that I think production that comes out of it.
Greg Dalton: Phil Williams?
Phil Williams: I like the definition of apply the innovation where the buildings are. And I guess I’m a little bit jaded. You know, we’ve even had the fortune to be -- I think that some of the world’s great building’s right here in San Francisco in the last decade, whether it’s the California Academy of Science, which is an architecturally beautiful building, double Platinum in terms of why it was designed and how it’s being operated, with natural ventilation and with radiant heating and cooling and all kinds of good things.
Or the SFPUC, San Francisco Public Utilities Commission Building here, which has operable windows, which has photovoltaics, which has raised access floor, which has, you know, black water recovery, gray water recovery, illustration of the energy and water consumption for the public to see. And I think if we’re not building a million cities, you know, a day or a million people cities per day, the fact is that we can still provide some of that innovation that others can leverage in and look at.
And I mentioned it before -- U.S. architecture is still the most highly -- one of the most highly valued export commodities that we have. Engineering, whether it’s earthquake or sustainability, is still seen as great. I think the construction expertise that all of us has in international firms, from the integrity, the delivery, and the reliability of U.S. firms, it’s a highly exportable commodity. And that being here in Northern California or in New York or in Boston or Austin or in Cascadia, wherever you’re talking about, it’s not isolated. It’s really an infectious kind of commodity; it’s important.
One term that I’d like use, and don’t credit it to me because I saw it in the late night television show, so I guess I can plagiarize as long as I tell people -- it’s a term called “future-ready” as opposed to “future-proof.” And future-proof means I’m going to build an eight-foot bunker and hunker out down and just pretend nothing’s going to happen. Where future-ready is tough. It’s like Greg said and like everybody said, “How do we anticipate the unknown? How do we leave room for improvement?” Because the part of the problem I always have -- it’s two years to design it and two years to build it, and in today’s rapid changing, it’s almost like I feel like I’m handling over a set of keys to somebody and let me build the next one better for you at the same time I’m handling over a set of keys. The buildings last for decades.
So I think our challenge, whether it’s flexibility in occupancy, flexibility in controls, you know, making sure that we’re giving good use to current materials, and they can be someplace else -- that’s really the challenge that we’re going to all face because we build legacies. It’s not like I can change a fluorescent one into an LED. It’s not, you know, three twists and I’m gone. Cars have a tendency to be disposable. Buildings -- the kind of commercial buildings we’re in -- aren’t. And I think that term “future-ready” is one that we all really need to try to embrace in whatever term we call it.
Greg Dalton: I’d like to pick up on the U.S. leadership point. I’ve spent a fair amount of time in China this summer and, you know, I look at the big buildings often designed by U.S. architecture firms, built by U.S. constructions firms, and yet there’s push back in the United States right now against some of this leadership, in particular the General Services Administration of the U.S. government has some baselines for LEED and there’s some pushback against that saying, “Oh taxpayers shouldn’t pay more for LEED.” Others push back from the chemical industry against LEED saying, “Well, LEED’s going to hurt our business.” So, let’s talk about this undercurrent that’s pushing back on LEED and all these things that we’re talking about trying to perhaps slow it down. Michael Deane?
Michael Deane: Well, by way of full disclosure, I sit on the federal GSA’s Green Building Advisory Committee, so -- which only means that I’m allowed to offer my advice to them directly. It doesn’t give me any special privileges other than that. The issues with LEED and the cost of LEED or achieving at certain levels, to me, is misplaced. There was a federal defense appropriation I think last December that said, “Military could not build LEED Gold or Platinum buildings unless they could demonstrate that it costs no more than a LEED Silver building.”
The fact is the Navy was just about to announce or had already announced that their new minimum standard was LEED Gold, and that was only after determining that it was a better value proposition and that in fact, it did not cost that much more.
Greg Dalton: And they own the building, they captured the cost of the life cycle, right? So…
Michael Deane: Right. Right. So, I think it was politically driven, and the impetus for the politics were -- and I may go out on a little bit of a controversial limb here, but why not -- the chemical industry in particular has been very much against the pending version of LEED that’s going to come out next year because it, for the first time, includes credits that don’t require, but give buildings the option of disclosing chemicals of concern that have a negative human health impact and/or avoiding chemicals of concern. And the chemical industry -- and this is the Chemical Trade Association, not the individual companies -- has come out against that as a “job killer.” So in a sense, they’re taking -- they’re picking money over human health if you want to parse it in a really blunt way, where the intent of the credit is to drive the market to say, “Look, you’ve got products that you produce -- many building products have chemicals that are harmful to humans in them.” The idea is to come up with a functionally similar or better product that doesn’t have chemicals that cause human health. That’s the way to drive the market. That’s the push for market transformation, and it has become -- that argument has been sublimated to an argument about economics.
And so now, the chemical people are joining with the earlier industries that were against LEED for similar reasons, which were the vinyl industry and the wood industry. So there’s this economic pull against environmental change when in fact, I believe, and I bet I could speak for everybody here, that I think it’s not either/or; it’s a plus/and -- that we move the market by creating better materials.
Greg Dalton: A group of companies in the architecture and design and construction sector wrote a letter to the GSA saying, “Let’s keep LEED.” I saw Gensler on there. I did not see the other companies. I don’t know if Webcor and SOM and Turner were on there.
Michael Deane: I chose to write an individual letter. I chose not to sign onto a form letter.
Greg Dalton: Okay.
Michael Deane: But I did write a letter.
Greg Dalton: And the others, I mean, do you think that LEED is something to protect, or you don’t want to get involved in the politics in the industry?
Craig Hartman: It is absolutely important. And has been discussed earlier in this panel that LEED isn’t necessarily a perfect end-all and be-all of itself, but absolutely the goals, they’re sort of a long trajectory of goals that are embodied in LEED, as one example, are the right things for us as a country to be embracing. And it is regrettable that things like the environment become politicized, and as regrettable -- where we are is a moment in our democracy. But there’s no questions if this is where we need to be going and has been -- and the fact that as LEED as one metric, has been embraced very broadly in the marketplace as a sign of a healthy environment.
And so, we see in our buildings, our clients are expecting this. And when it becomes expected in a general populace, the government, if not LEED, and will certainly follow. We, about eight years ago, decided we’d have a meeting here in San Francisco Committee Meeting at Presidio and decided that in our practice at LEED, so we would do no buildings in the city of San Francisco that weren’t at least a LEED Gold. And with all the private -- we turn away client, if I lose clients whatever -- if we lose a single client, and as Phil said, now in this coming year it’s going to be a law anyway, so -- and frankly, it’s not that difficult to achieve LEED Gold in San Francisco. (0:48:00)
But it’s absolutely become -- this is an expectation in the marketplace.
David Gensler: I think Craig is pointing about the fact that LEED is not the objective. The objective is to use our resources more intelligently. And I think -- I don’t know about SOM but in our firm, we have a whole generation that is extraordinarily passionate about this issue. The --
Greg Dalton: Rabid, you say.
David Gensler: No, I think. You know it’s -- there’s a religious fervor at some level about this issue in our younger staff, particularly for the last 15 years or so. We’ve had these grassroots effort to have a higher level of commitment to sustainable design, to intelligent, responsible use of resources, to water, air, energy, you know, intelligent design solutions. And it’s the history of design -- it’s to solve problems and to use resources intelligently. But right now, it’s heightened, and particularly in our young staff, I think people under 40 seem to be, you know, very aware and committed to this.
And so, if you look at our standards -- nothing to do with LEED. Our minimum standards for design are at a very high level. We have what we call “green speck” which goes out with every project. Our vision is that if we can improve our entire portfolio’s performance, you know, 10% or 20% or 30% above code, we can have a tremendous impact on the world, irrespective of whether we have a LEED Platinum or Double Platinum or anything. That’s not the way we’re going to get to where we’re trying to get to. What we’re trying to do is raise the bar for everything. And there will always be, you know, specific instances where we can stretch the envelope, but it’s about raising the entire platform together.
Greg Dalton: I hear your point that LEED’s not everything. But if LEED gets slowed down and it’s the industry’s standard, it could slow the industry -- Phil?
Phil Williams: Sure. Well, I don’t know look government to be a leadership. Okay.
[Laughter]
Greg Dalton: You know, 27% of the LEED buildings -- and again, LEED is not everything but it is a standard. Twenty-seven percent of the LEED buildings are public sector buildings. So it’s a --
Phil Williams: Yeah. But if you do the math, that means that over 70% are private, that up until recently weren’t -- and some very select areas weren’t even mandated. So the market is driving it. It’s not just the small autobahn society or the corporate one. And I think from that perspective is that it’s nice of the government -- I think it’s important that the government does -- I’m a taxpayer, I live here, I expect my dollars to be spent wisely over the long term. It’s been politicized. The only thing that’s been beat up more than the GSA is the EPA. And I think it’s those initials that have a tendency to get political fervor depending on which side of the isle you’re on.
But one of the things -- and I think everyone here embraces in a different one -- we’re not just building projects for other people. We’re businesses. We have businesses. And I think as you do your work and as we do our work, one of the things that we’re measuring is we did our carbon footprinting. We had an opportunity to look at our energy and the paper and where we fly, and then we did what we build. We recognized that Webcor’s carbon footprint, our greenhouse gas emissions -- 0.6%. Just over one-half was the operation of our business -- 99.4% was what we built.
Greg Dalton: And then how did they use it?
Phil Williams: And so far, our obligation is we’ve looked at that supply chain and I think that’s expanded past LEED. LEED has given us the opportunity to open our eyes but its not necessarily show in the spotlight on where our real work is as professionals to say, “How do I build that square footage at half the carbon that I did before?”
Michael Deane: No, I agree completely. Any major builder and I’d say any major architect can design and build LEED buildings today. We’ve been doing that for 10, 12 years. But where I’m spending my energy like Phil is, you know, we just made a carbon emissions reduction commitment that we set in 2006 for our offices.
But looking at our field operations is manically complex and we weren’t even able to address it. But our field operations -- how we use water, how we use energy, how we use fuel -- and our supply chain, which is far bigger than our direct footprint is where the work is. And I think that’s the work for the next 10 years, honestly.
Greg Dalton: Michael Deane is chief sustainability officer at Turner Construction. Our other guests today are David Gensler, executive director of Gensler; Craig Hartman from Skidmore, Owings, & Merrill; and Phil Williams from Webcor. Let’s have our audience’s questions. Yes, sir?
Male Participant 1: Yes, gentlemen. The first question is -- well, only question [Laughter] -- all of your firms to some degree I’m sure deal with building information modeling and it’s nothing new, but, you know, Building Smart’s definition, not I’ve got --, how will you find -- what are the challenges you were finding of BIM as far as the process? And then how are you helping your clients find ways of using that data and upkeep all throughout the building’s life cycle to get a max return on investment?
Greg Dalton: Phil Williams?
Phil Williams: I’ll jump in the beginning -- I mean building information modeling started with us about 3 years -- or 10 years ago with conflicts, and we rapidly evolved it to -- it’s not just a colorful thing on a screen its an entity. So now we can schedule with it, because now it’s a known cubic yard of concrete. Where has it got to go? What steel is in it? Where’s the concrete coming from? Where’s the aggregate coming from? We do our material resourcing from it. We look out for procurement. And what we’re rapidly doing is also using these wonderfully coordinate drawings -- the as-built -- in the facilities management models.
One of the analogies that I use is you’ve got kids out there -- the video games that they use in Madden 2012 have got more data regarding the NFL and players and the color of their cars and how much money they make and what their fourth down average is than we know how to run our buildings.
So, what we’re doing is we’re not looking at the building industry to supply this visual interactive tool; we go to the gaming industry. I’ve got the data. I’ve got the model. now, to give my building engineers the ability to integrate that in real time and maybe give you some what-ifs scenarios and what the weather is today for tomorrow, they don’t have to be a PhD, Lawrence Berkeley lab guys. They just got to know what I do today to fix tomorrow. I think it’s that kind of integration of technology that’s key, not just what we build, but it goes in the design, the construction, and the longevity. I think that’s where building information modeling is headed and needs to be.
Greg Dalton: If John Madden joins the board, your companies -- the meetings will be a lot more fun; that’s for sure. [Laughter] Let’s have our next audience question.
Male Participant 2: Hi. I know all of you -- all your companies are leaders in your industries. What are you seeing as a leading innovation that you’re exporting either into the market or internationally?
Phil Williams: I’d say for us it’s net-zero energy. It’s the current stand. We have a small but growing portfolio of net-zero buildings based not just on design calculations but on the building performance, and they range from bank branches to schools to the municipal office buildings. And taking the lessons learned from those buildings and sharing them with other project teams and other projects so that every building can benefit from the best examples that we have is one of the things we’re doing. We’re also -- I personally, and I think a lot of us are very concerned about water, so, looking at that. But having big portfolio buildings where you can take lessons learned from best practice. And right now, as I said, that’s net-zero energy.
Craig Hartman: I was just -- I was just to add to that for a moment.
That -- it was mentioned that -- I think Phil said that architecture in the U.S. is a major export business without question. Now, David and ourselves at SOM are doing right now, I think in San Francisco, about half of our workers are in California and about half of our workers are in China. And so we are definitely a major export business in that regard, at least as architecture goes.
And I think in terms of what we are I think bringing mostly to the table right now in addition to that -- we view basically San Francisco as kind of a petri dish, because it is a place that we can really use some innovations and the government supports the ideas that we’re doing. And so, we’re exporting mainly those ideas to China especially about the way you think about buildings holistically in our environment. So, all of us at this panel, obviously, are designing buildings that deal with the reduction of water and energy to the lowest possible we can moving towards net-zero at some point in the future.
But equally important is to think about how these buildings relate to the cities and how we make cities themselves that are performing at this very high level. And so, this is I think an area of focus that we are probably most interested in right now in terms of how we’d make the greatest impact.
David Gensler: I think for us, like -- the urbanization of the developing world is what’s driving the export market for our designs. And basically, they have to leapfrog a whole generation of development and evolution and capability building in their countries to get to world-class level design -- whether it’s the aesthetics, whether it’s steel and glass, whether it’s LEED and sustainability -- the whole package is what they are looking for us to do. And so what we’ve done is we’ve actually gone to China; we’ve gone to Korea, and India, and South America, and Brazil, and Costa Rica, and in the Middle East, and we’ve started to build our organization in those countries. And we export design talent, but we also build communities that can, you know, be made up of local nationals, who will be able to design the future of their countries.
So, we’re slightly different than most design firms in that we’ve been willing to invest in building a footprint in countries, around the world to help developing countries urbanize as they grow and develop.
Greg Dalton: Let’s have our next audience question.
Male Participant 3: Arthur Young, communication management in the Climate Reality Project. As you know, USGBC’s LEED protocol mandates reviewing every aspect of LEED every two years. How do your businesses manage, monitor and deal with change every two years in an industry that is far from simple?
Phil Williams: I’m going to pick up on my comment of future-ready. What we try to do is allow that energy water to effectively be monitored. And I think because if you had no fuel gauge, if you had no speedometer, if you had no oil light, go to the mechanic. And many times, those kinds of things are at handover at best so that the ability to get independent commissioning, the ability to provide instrumentation is key. It’s that future-ready component for us.
We’re not in the building management business afterwards. And I think from a business perspective, one of the things that we’re toying with, and I think maybe -- I don’t know if we should challenge each other. This is sort of that -- I’m not going to bet, you know, lobsters versus crabs versus clam chowder, but I think we ought to go to guaranteeing building performance rather than warrantying a building. And I had somebody challenge me. They said, “Phil, what’s the difference between warranty and guarantee?” Warranty is repair or replace. Guarantee is satisfy. And I think that’s our ultimate challenge, is to satisfy the energy and the comfort and the water goals, and data is going to help us that.
But I also think this comprehensive design approach and that we all share in the outcome, and we need an owner here by the way, because that’s the other triad. I think three is a powerful number. It’s nature’s best resource. It’s stable, you know. One leg you fall over; five legs is always rocking, three is that perfect component. I think we need an owner here because they’re an instrumental part of what we build and design and what they pay for. And then I think that’s where we can go to guarantee that versus warranty. And that’s where you get loyalty, and that’s where you start to build buildings we all have a longer than 18-month time frame, 36-month tenure payback.
Greg Dalton: Good point. Next time, we’ll have an owner, I guess. Let’s have our next audience question. Yes, sir?
Male Participant 4: How would you recommend fixing the controls industry? I think we’re all familiar with buildings that built relatively recently -- they’re very high-tech. The panel talked about technology and controls earlier, and yet the heating systems run in the middle of the night and they don’t run during the day when they need to and all those sorts of problems. It makes me think of the number of people who knew how to program their VCR in the ‘90s is about the percentage of building managers today who actually know how to control their buildings.
On LEED Platinum space, I’ve been in the U.S. Green Building Council headquarters. It actually has, you know, dynamic shading that adjusts to daylight levels. And that thing has never worked, right? (Laughter) The staff absolutely hate it and, you know, there’s glare and there’s, you know --they’re turning the lights on trying to find out how to turn the lights on when the shades are down and they don’t need to be.
So, as we get higher and higher tech, there’s still a problem of operationalizing controls and getting it right. So, how do we solve that problem?
David Gensler: I think we’re an industry in transition.
And, you know, we also are an industry that I call a virtual corporation industry of contractors and engineers and architects and consultants, you know, that all come together around a project, and then they disband and come together around to the next project. We don’t have fully integrated organizations. If we were going to, you know, guarantee a level of performance, it would probably be much more likely that a design build firm would be willing to take that kind of a challenge on.
And frankly all of us, I think, are questioning now what are the optimal delivery models for today. There’s different delivery models around the world, and we’re experimenting ourselves with the design build in certain marketplaces. But my point is really that when you innovate, you’re going to have -- you take a risk. You don’t have certainty and what we’re seeing is we try things, we model them, we say that, you know, we think this will be the performance and we’ve -- sometimes we find they perform higher, and sometimes we find that they perform less. And the next building we build will be better. And the -- we’re getting technology integration in the buildings where the systems are starting to take more responsibility for managing the performance of the building and it’s not based on talent that doesn’t have the skills to manage a building. So that’s one area where, I think, we’re going to see some really significant change over the next decade.
But it’s going to take time as we evolve as an industry. We’re not built to build the same thing over and over and over again. Every project is custom. Every project has a different stakeholder base. Every project has a different community that’s doing the projects. So, it’s an industry that has its strength and weaknesses in that model.
Phil Williams: It’s true and it’s also a fact that buildings remain the world’s largest handmade objects. And the fact is, unlike a car that’s prototyped and before you even go in production, you’ve tested all its systems. With building, you have hundreds, sometimes thousands of individuals involved, not only in design but also in the construction of the pieces in very, very difficult field conditions, obviously.
So it’s an imperfect environment in which to implement these things, but I do think that a lot of the things that you point to are certainly on a trajectory of improvement. And we’re seeing things today that we could never have done even 15 years ago in terms of controlling environments. But you’re right. Every building needs to have an operating man or have to have people who know how to operate these facilities because that’s where in the end, they fail or they succeed.
Greg Dalton: Let’s have our last audience question. Yes, sir?
Male Participant 5: So building codes in the U.S. are very prescriptive, and they often limit innovation particularly in sustainable buildings. So I just appreciate the panel’s thoughts on this challenge.
Craig Hartman: We have to build the code, right? I mean that’s the lowest standard of (laughter) -- well, the good part of that code is -- I haven’t seen -- I mean in some respects they let us put more area, right? They will let us -- there is no minimum energy requirement in the building thank goodness, you know, along those lines. We’ve gotten away from plumbers worrying about waterless urinals. I mean there’s been some good technologies.
I think the slowness of the industry sometimes have to do with buildings are primarily also life-safety components -- they can’t burn, they can’t fall down, you have to have egress, and there’s a lot of things along those lines that from a generational perspective, most of the time, the senior people in organizations have got a different perspective many times, especially on the public side -- isn’t necessarily known as the most innovative market segment.
And so, I think from our’s working within the system is the best way to do it, whether it’s better smart or concrete and re-bar and testing it out and having the patience to do it. But I also think it also means that we have to help develop new standards because codes rely on proven industry standards.
And unless we get behind standards that are near-perfect and will -- and definitely LEED does, I think it’s an excellent one. If we can help not just complain, but physically lend our personal time to help writing new standards and that governments can adopt, whether it’s the GSA, EPA, San Francisco Fire Department, I mean, you know, let’s face it -- operable windows in the San Francisco high-rise are extremely difficult, because the Fire Department’s trying to preserve life, which I can’t argue with. But -- so how can we use intelligence to help them understand that there’s ways to get both?
It’s not -- whoever said it before, it’s not either/or, it’s and; and that’s how, I think that we start to transform somewhere where we’re at. And it’s places like San Francisco, frankly, that sets this bellwether standard for other cities. It’s as regressive or progressive as you might think this place is, San Francisco, and even California, is really viewed globally as the most responsible place in the United States to look -- whether it’s green technology, high-tech technology, social media, or fuel. And so, I think if we all live here and our zip code is somewhere around this area, we’ve got an obligation not just to ourselves but to the U.S. and the rest of the world, if they’re looking here, to be as good as we can -- and experiment where we need to, right, in those kinds of safe environments.
Michael Deane: You know, I think -- just one word, I think that recently there’s been a lot of work done in codes. There’s the International Building and Construction Code. There’s CALGreen. There’s the New York City Building Code, and on and on, there’s ASHRAE 189. So, a lot of that work has been done, and now we just need the municipalities to adopt them.
Greg Dalton: Before we wrap, I want to ask one quick question. I’ve seen lots of cool-looking pictures of urban agriculture -- buildings with farms on them. Is that science fiction? Or is that really going to happen anywhere? Craig Hartman?
Craig Hartman: Well, I was suggesting. It is happening. It already is happening, and we’re doing two very large projects here in San Francisco. One is Treasure Island, the other is Parkmerced, both of which will have significant urban farming as a part of the operations. And these aren’t places -- farms with fences going around them. These are new kinds of farms in which they have a kind of pedagogic road which -- they’re almost like productive parks. And you could walk in, you observe these things.
So that’s definitely happening. We’re still pushing for rooftop, but that’s a little bit out there yet. Most of rules are just green living rules, but I think that there’s -- again, this is a cultural thing at this point, more so than it’s a market-driven thing because of the interest especially, I’ll say in the Bay Area and California in general, about locally sourced everything, and food of course being the most basic one. And so I think there’s a real interest in this in terms of having it right near us.
Greg Dalton: Our thanks to our panel today. Phil Williams is vice president of Webcor Builders; Craig Hartman, design partner at SOM; David Gensler, executive director of Gensler, the design firm; and Michael Deane, chief sustainability officer at Turner Construction. I’m Greg Dalton. Thank you, all, for coming today.
[Applause]
[END]